Small adjustments add up to big savings at West Fraser
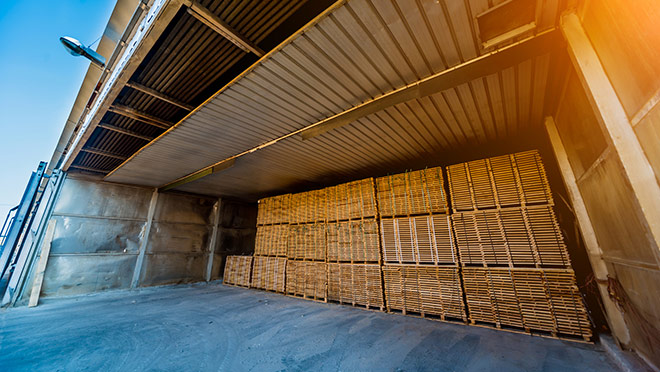
A long-term commitment to energy efficiency
West Fraser is a diversified wood products company with more than 60 facilities in Canada, the US and Europe. Working closely with Indigenous communities to sustainably manage forest resources, West Fraser has just celebrated planting two billion trees.
Since 1955, the company's products have grown to include lumber, engineered wood (including OSB, MDF, and plywood) along with pulp, newsprint, wood chips, and renewable energy. West Fraser's products are used in home construction, repair and remodelling, industrial applications, papers, tissue and box materials.
For decades, energy management has been a big area of focus for West Fraser, especially in B.C., where BC Hydro incentives have helped them make a variety of energy-saving upgrades.
"We started partnering with BC Hydro around 15-20 years ago, and we've been working with their Strategic Energy Management (SEM) program for about 10 years," explains Perry Ghuman, Energy & Carbon Section Lead, who heads a team of Energy Managers across West Fraser's pulp and timber facilities. "Initially, our motivation was to reduce our electricity costs, but we also want to make a big effort to reduce our carbon footprint."
"It's not just BC Hydro incentives that have helped West Fraser identify and implement some clever solutions," says Sam Walker, an Energy Coach at Stillwater Energy who works with West Fraser. "The whole workforce is empowered to help suggest and explore new ideas."
Kal Sahota, Forestry & Large Industrial Key Account Management at BC Hydro agrees. "We're always really impressed with some of the best practices West Fraser have in place," explains Kal. And at the Williams Lake facility in particular, we love that their culture enables employees to identify areas for improvement with an open-minded management team."
Empowering the team to save power
With a workforce so passionate about reducing energy usage wherever possible, West Fraser has been able to make a lot of seemingly small improvements and ongoing adjustments at its Williams Lake facility that collectively add up to some impressive savings, including:
Dust collection systems are rebalanced annually
Like any timber mill, the facility has large dust collection systems with many energy-intensive fans running all the time. Dust inevitably builds up over time in the ducting, causing the fans to work harder. Ducts are checked once a year to ensure the fans are only pulling the minimum amount of air needed through a process called 'rebalancing'. Rebalancing analyzes air pressure along the main duct and all the branches to find any blockages.
Equipment is interlocked to shut off automatically – and shut down during non-production hours
Wherever possible, compressors, drives and conveyors are set to detect when they're running unnecessarily (such as during coffee breaks) and to power down outside of working hours.
Air compressor heat is redirected to heat interior spaces
The heat generated by mill machinery is recycled and redirected to offices and breakrooms, instead of being wasted.
Air compressors are regularly checked for leaks
Since air compressors aren't just working in the mill, but also providing heat for other parts of the facility, it's important to be constantly checking for leaks. The facility has a formal annual leak audit, but employees are also empowered to proactively identify and fix leaks all year round.
Dry fire sprinklers have a dedicated compressor
It's standard practice for mills to use plant air to pressurize their fire systems. However, during non-production hours, this means that they're still running full-size compressor(s) just to drive the fire system. At the facility, a smaller, dedicated fire sprinkler compressor was fitted for much more efficient protection 24/7.
Kilns are dialled into specific needs
Lumber is carefully heated in a kiln to remove moisture. As you'd imagine, it's a delicate procedure and mistakes can be costly. Most modern kilns have variable frequency drives (VFDs) that adjust the speed of the motors and keep the temperature constant. However, many of these kilns are often not properly controlled based on each load. This is where West Fraser's workforce can offer a solution.
"The best place to start is with the kiln operator," says Kal. "They know their kiln better than anyone else and can usually provide the specific data needed to know if the VFDs are working effectively. So far, BC Hydro has partnered with West Fraser on a couple of kiln projects in the Lower Mainland. Drying times are different further north because of the climate, so in the future, we may also explore running a kiln optimization study across all regions."
Sharing the knowledge
While West Fraser's deep partnership with BC Hydro has led to many efficient practices at its Williams Lake facility, not all regions are able to offer the same support.
"Many provinces just don't have the kind of incentives that BC Hydro offers, and in some areas of the US, there don't appear to be any incentives available at all," explains Perry. "So we share the best practices we learn here with our other locations across North America – and empower those teams to follow the same procedures we do here."
Do you need help with a project?
If you'd like to explore our 100% funded industrial studies or are interested in our Custom Incentives, contact your Key Account Manager or Regional Energy Manager, or call us at 604 522 4713 in the Lower Mainland or 1 866 522 4713 elsewhere in B.C.