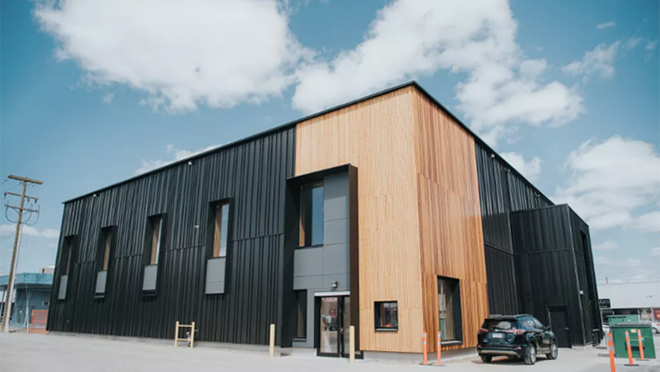
Prince George university sets a high standard as a Clean Energy Champion
Part of a series on BC Hydro Clean Energy Champions: businesses, homes, and institutions – large and small – recognized for reducing their reliance on fossil fuels.
Of all the green building certifications out there, the Passive House standard is the one that most focuses on the design of a building's envelope – including insulation, windows, and airtightness – to minimize heat loss and gain. Certified Passive House buildings use up to 90% less energy for heating and cooling compared with standard buildings, and use up to 70% less energy overall.
The University of Northern BC in Prince George has done wonders over the years to save electricity and cut greenhouse gas emissions. So it made sense that they’d literally push the envelope by experimenting in Passive House techniques that are all about making buildings energy efficient, comfortable, and environmentally friendly.
UNBC garnered international attention when it built its first Passive House facility– the Wood Innovation Research Lab (WIRL) in downtown Prince George and earned Passive House certification in 2018. Designed to enable researchers to discover novel materials and techniques for the next generation of tall wood buildings, it set a new standard for air tightness for North American buildings: a score of .07 air changes per hour that surpassed the Passive House requirement by nearly a factor of 10.
Then a near disaster – an explosion and fire in a neighbouring building that burned a hole through the wall of the WIRL and set off the building’s fire sprinkler system – produced another revelation. Tasked with the building’s restoration, UNBC replaced panels on the fire-damaged wall and, upon inspection of an adjacent wall that had been soaked by the sprinkler system, discovered that it had quickly recovered.
“The building envelope team were surprised to find that the wood inside that wall was drier than the wood that was inside the rest of the building,” says David Claus, UNBC’s director of facilities management and capital planning. “It had done what it was supposed to do. It dried itself out all on its own.”
Delighted by their first foray into Passive House design, UNBC pursued (and landed) Passive House certification for its new Facilities Management Building that opened in 2021. And Claus and his team moved in, with the idea of learning firsthand what works best, and what may not work best, in a Passive House building.
The team moved in while the building was still being commissioned and not all services were connected. They found that temporarily running hot water through a garden hose from the power plant next door and then through a heat exchanger and a heating loop was enough to keep the building warm. The building is so airtight that heat generated by the building’s occupants, photocopiers and other office equipment means that cooling, and not heating, is the primary need.
“The building tends to need cooling just about every day of the year,” says Claus. “Water from the power plant next door comes out of the ground at between 6 and 10 C, depending on the time of year, we run it through a heat exchanger, and we essentially get free cooling for this building.”
Claus says he’s trying to make the case that all new UNBC buildings should be built to the Passive House standard. For now, the latest experiment is a Passive House retrofit a three-hour drive south of Prince George, at UNBC’s Quesnel River Research Centre. Instead of building new, UNBC is looking at adding onto an existing storage building – the so-called “boat house” – to transform it into a research facility wrapped in a new layer of insulation and air barriers.
“It’s kind of like putting on a big winter jacket,” he says.
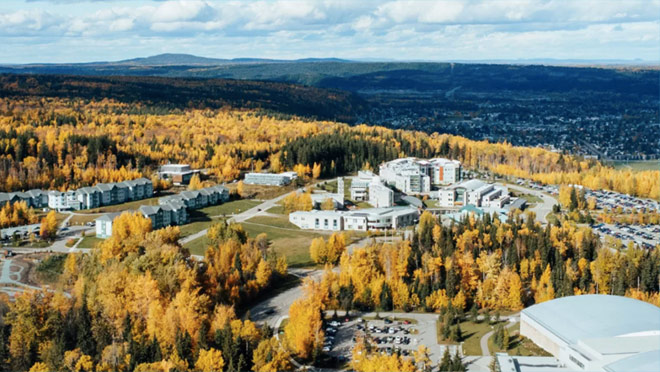
'Closer to a race car': UNBC tunes up, upgrades
In his nearly 15 years at the University of Northern BC (UNBC) in Prince George, Claus has developed a flair for metaphor to help explain the university’s bold and strategic approach to energy efficiency and carbon reduction.
To Claus, it’s not a stretch to compare continuous optimization of building systems to the challenges of owning a car.
“You get your car tuned up every once in a while, and if you're like me and you don't really look after your car, that happens very infrequently,” says Claus. “It gets me from A to B. But [at UNBC] we take the view that we want our buildings to perform better than the family car that gets me back and forth to the school every day. We want it to be closer to a racing car. So we're continually measuring it and going ‘OK, are we at peak performance, or can we eek a little bit more out of this?”
Consulting with BC Hydro and leaning on available incentives, UNBC’s first foray into continuous optimization tweaks – 79 measures ranging from building occupant schedule revisions to upgraded controls of ventilation, lighting, hot water, and air exchanges – netted annual savings of nearly 14% in electricity use and 23% in gas use.
And the energy savings paid off. UNBC raced from zero-to-payback on the costs of those implementation measures – implemented from 2012 to 2017 – in a lightning fast 1.1 years.
So they did it all again.
Reconfirming 73 of the initial measures, and acting on another 29 new measures, they saved another 1.8 million kWh per year in electricity between 2020 and 2023. They also saved 43 tonnes of CO2 annually by using less gas.
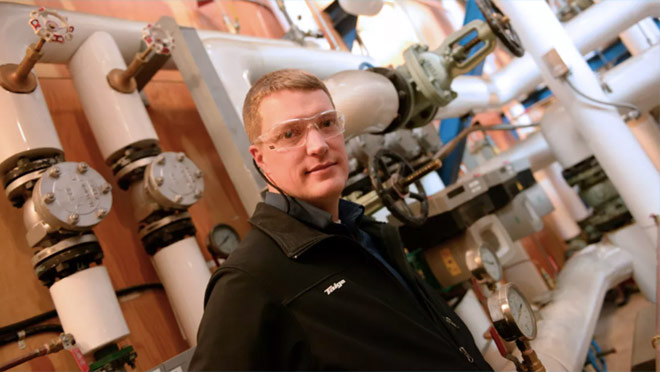
'Savings roll on with tweaks and district energy
Claus and his team won’t give up on the idea of that race car, sometimes opting to build it from the ground up. In addition to continuous optimization, UNBC has been big on innovation with the likes of Passive House building. They also launched a bioenergy plant in 2011 that uses waste wood to heat 85% of the campus.
“We keep experimenting,” says Claus, who’s also building a Passive House residence for his family. “For me, it's way more interesting to be going after the next thing. We’ve fortunately been able to hire staff who are able to maintain what we've already done while asking ‘What else can we do?’”
There’s always more. And making it all possible is a “revolving loan” strategy Claus successfully pitched to UNBC’s finance group years ago. It’s all about using energy cost savings from efficiency projects to invest in future projects, and it remains the facility management group’s go-to strategy.
“It enables us to do a lot, to the point where we're limited by our capacity to plan out the projects, and not by the funding that we have,” he says. “That won't hold true if we're planning a whole building envelope on a great big research lab. But for the work that we've been doing up until now, it’s been able to cover a lot of things and keeps it moving.”