Explore your energy usage with Operational Energy Analytics
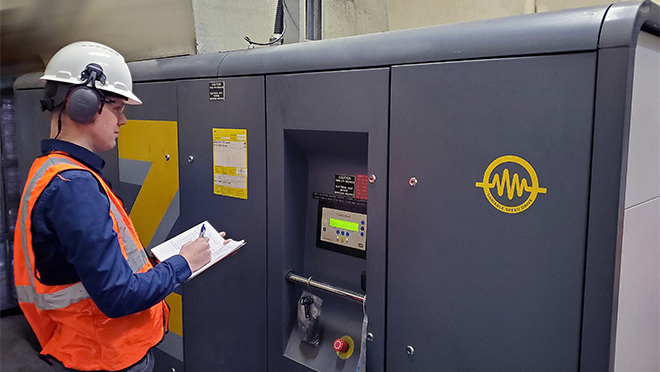
Free service can point you towards savings in your system
If you're an industrial customer, you may be eligible to take advantage of one of BC Hydro's Strategic Energy Management (SEM) programs. We recently took a look at how to generate energy saving ideas by participating in the Industrial cohort program. Now we're going to focus on another SEM program designed for smaller customers: our Operational Energy Analytics (OEA) program. It's a free service that shows you how to better understand your system to make year-on-year savings.
What is OEA?
OEA provides an energy assessment of your facility designed to identify best practices and secure low-cost or no-cost savings through operational energy conservation measures. The cost of this assessment is fully covered by BC Hydro to help you to:
- Get a better understanding of energy usage within your organization
- Start introducing energy management principles to reduce consumption and save money
Why your business should participate
OEA comes with lots of benefits. First, as we've already seen, it's free - BC Hydro pays for your assessment. By taking part in the OEA program, your organization will also:
- Gain access to industrial energy management experts
- Become more familiar with every line item on your BC Hydro bill
- Receive practical energy conservation recommendations - often supported by BC Hydro incentives
- Earn a participation bonus of $0.01 per kWh (up to a maximum of $5,000) based on your first year's savings
- Immediately start saving energy and money
How does the OEA process work?
Every OEA is conducted by Panevo, an independent engineering and energy conservation consultant. Panevo has partnered with BC Hydro since 2014 and has successfully delivered over 100 OEA audits. While the savings and recommendations from OEA can differ widely, the process is largely the same for every business. Here's what you can expect:
- Bill review: An assessment of your recent BC Hydro bills designed to determine any line item savings potential, such as your power factor or demand charges
- MyHydro analysis: A review of your MyHydro / smart meter data. This is mapped against operational profiles and equipment utilization to highlight usage profiles and identify potential conservation measures
- Site investigation: The onsite investigation can last up to a day, reviewing approaches to energy management with key stakeholders and auditing your most energy-intensive systems. These usually include:
- Process and manufacturing equipment
- HVAC (heating and cooling)
- Pumps, motors and drives
- Air compressors
- Lighting
- Monitoring campaign: Meters and sensors are temporarily deployed to track the energy use of specific equipment and quantify potential savings
- Conservation trials: When a potential energy conservation measure is identified, Panevo can support with determining the benefit, creating the business case and recognizing any impact
- Sustainment plan: Your sustainment plan features guidelines on energy management best practices and Standard Operating Procedures (SOPs) to sustain real energy savings over time
- Sign-off and next steps: Signing off on your sustainment plan commits you to achieving the savings and starts your bonus incentive application process
What kind of savings can you expect?
OEA recommendations aren't necessarily going to require expensive infrastructure upgrades. There's plenty of potential to generate some big savings just by changing behaviours or installing cost-effective controls. Panevo's CEO, Craig Holden, explains: "We see some businesses achieving double digit percentage savings in energy through operational measures. For some customers, it's possible to secure significant savings by implementing simple controllers, such as occupancy sensors for lighting or timers to switch off equipment outside of operating hours, for example air compressors or HVAC."
Some examples of savings that Craig and the Panevo team have helped secure over the years include:
- A greenhouse that minimized fan operation to reduce energy usage by 17%
- A manufacturing facility that altered compressor set-points and implemented an equipment switch-off plan during breaks to reduce energy usage by 12%
- A food and beverage processing facility that optimized their compressed air generation to reduce energy usage by 10%
"Switching off equipment when it's not actively involved in production seems obvious, but can be overlooked," says Craig. "One customer example included a dozen welding units that still consumed power even when in standby mode. Switching off the units that weren't required resulted in savings of over 20,000 kWh per year."
Reviewing equipment set-points is also an area where immediate, zero cost savings can be made: "We've seen air compressors operating at 130 psi, when 110 psi or less would suffice. In some applications, it's possible to incrementally reduce the compressor set-point over a period of time until you find the sweet spot," Craig suggests. "Typically for every 2 psi set-point reduction, you can expect a 1% saving in compressor power. And you'll see significant savings if you combine this with an effective leak management campaign."
How to get started with OEA
If your industrial facility consumes between 0.5 and 4 GWh of electricity per year (roughly $50k to $400k), then you're eligible to take part in OEA. Find out more about OEA at bchydro.com. You can also contact your Regional Account Manager or the BC Hydro Business Helpdesk:
- industrial@bchydro.com
- 604 522 4713 (Lower Mainland)
- 1 866 522 4713 (Elsewhere in B.C.)